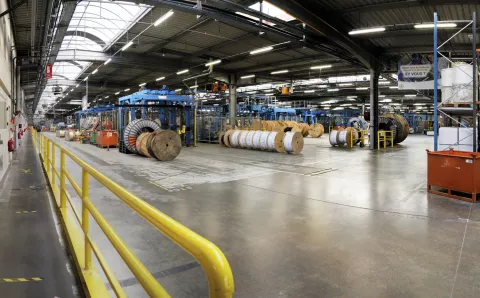
ACOME intègre les technologies HEMERA de l'industrie 4.0 sur son site industriel de MORTAIN
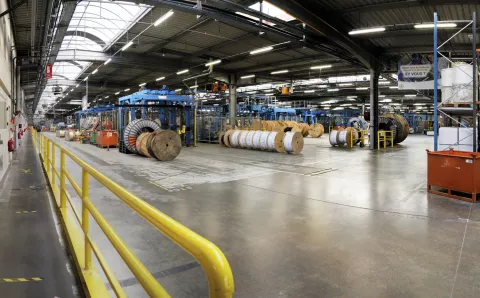
ACOME, en tant qu'industriel performant de produit de haute technicité, doit maintenir ses méthodes de production conformes aux normes de l'industrie 4.0. Cela implique l'intégration de technologies de pointe HEMERA telles que la numérisation et l'automatisation pour optimiser ses processus. En adoptant ces avancées, ACOME vise à rester compétitif et innovant sur le marché. Ainsi, l'entreprise s'engage à maintenir son leadership et à répondre aux exigences croissantes de l'industrie.
L'industrie 4.0 : Une nouvelle vision pour l'avenir
À l'aube de la quatrième révolution industrielle, l'industrie intègre les avancées numériques au cœur de ses processus de production. Cette ère, baptisée industrie du futur, repose sur la numérisation, l'automatisation et l'intelligence artificielle. Ces avancées offrent des opportunités de progrès, de compétitivité et de croissance. Remontant dans le temps, la première révolution a débuté en 1765 avec la machine à vapeur, suivie en 1870 par la production de masse grâce à l'énergie électrique et pétrolière. En 1969, la production automatisée a émergé grâce à l'électronique et à l'informatique. Aujourd'hui, la quatrième révolution intègre l'internet des objets, l'IA, le cloud et le big data, redéfinissant l'industrie. Ces avancées ouvrent de nouvelles perspectives et défis pour le secteur.
Un déploiement basé sur nos savoir-faire
ACOME avec la solution HEMERA a récemment intégré les technologies du numérique à plusieurs de ses ateliers de production, ce qui mène aux avantages suivants:
- Mesurer en temps réel nos performances de production
- Avoir une vision globale et en temps réel de l'état au parc industriel
- Capitaliser les données machines et de faire de la standardisation
- Détecter les défauts de production au plus tôt dans le processus de fabrication
Cette intégration numérique a nécessité le déploiement d'un réseau de communication entre chaque machine. C'est en se basant sur notre savoir-faire en terme de câblage, sur l'expertise de nos équipes terrain que nous avons pu tester dans ces ateliers différentes configurations d'architecture réseaux et valider nos produits afin d'arriver à une solution fiable et pérenne.
LES BÉNÉFICES DE LA SOLUTION MISE EN ŒUVRE
- Utilisation des chemins de câble existants : la compacité des câbles optiques a évité de recréer du cheminement, les câbles ont trouvé leur place dans l'existant.
- Déploiement progressif : grâce au concept du câble à accessibilité permanente PACe, nous avons pu déployer la rocade optique dans un premier temps et ensuite connecter les machines au fur et à mesure en fonction du projet.
- Pas de sous-répartitions : malgré la taille des bâtiments et leur éloignement les uns des autres, il n'a pas été nécessaire de créer des sous répartiteurs grâce à la fibre optique. L'implantation d'une unique baie 19 pouce 42U a été nécessaire.
- Insensibilité aux perturbations électromagnétiques : contrairement aux câbles cuivre, la fibre optique est insensible à la pollution électromagnétique émise par certains équipements.
Témoignage ACOME : Stéphane Deslandes, responsable maintenance et Rodolphe Agasse, technicien au sein de l'équipe maintenance
Stéphane Deslandes :
Cette initiative s'inscrit dans l'évolution des métiers de la maintenance industrielle, utilisant les technologies de l'information pour anticiper les opérations de maintenance et éviter les pannes. L'objectif est de réduire les interventions curatives au profit de maintenances préventives voire prédictives, nécessitant la collecte des données machines via notre infrastructure fibre HEMERA. La mise en réseau a permis des progrès significatifs dans la planification des maintenances, en permettant une distinction plus claire des organes des machines et l'implémentation de compteurs de temps de production. Certaines lignes stratégiques font l'objet d'une surveillance accrue pour minimiser les temps d'arrêt. Grâce à l'accumulation de données, une démarche d'analyse est entreprise pour corréler les événements qualité et process, permettant une transition vers la maintenance prédictive. Cette mise en réseau constitue la première étape de la transformation des métiers de la maintenance, nous dotant d'un outil fiable de suivi en temps réel et de détection précoce des dérives grâce à l'intelligence artificielle, permettant ainsi d'anticiper les opérations de maintenance et d'éviter les défauts de production.
Rodolphe Agasse :
Les remontées d'alarmes sont centralisées sur la supervision, alertant ainsi l'équipe en temps réel et facilitant la préparation des interventions sur les machines distantes. L'aide à distance est désormais possible, permettant à un technicien sur site de solliciter un expert distant avec les mêmes informations. En résultat, malgré un nombre d'opérations accru, celles-ci sont mieux anticipées, planifiées et les temps d'intervention sont respectés, libérant ainsi du temps de production.